基于机器学习的预测性维护:防止设备计划外停机
发布时间: 2023年06月13日
标签:
在现代工业领域,非计划停机是一项令人头疼的问题,它导致生产损失、利润减少,并给运营团队带来巨大的压力。然而,基于时间的维护策略并不能有效应对所有设备故障,因为大部分故障表现出随机模式,难以准确预测和预防。
在这种情况下,基于机器学习的预测维护成为一种强有力的工具,它能够提前识别设备故障,并采取相应措施,以避免非计划停机的发生。基于机器学习的预测性维护是一种利用机器学习算法来预测设备故障并采取相应措施的维护策略。它不仅仅依赖于设备的使用时间或预设的阈值限制,而是通过分析数据中的模式和异常来提前识别潜在的故障事件。
预测性维护的核心思想是在设备正常运行期间收集大量数据,并通过机器学习算法对这些数据进行训练和分析。机器学习模型可以学习设备的正常行为和特征,并在未来出现异常时发出警报。这样,维护团队可以及时采取措施,避免设备故障导致的非计划停机和生产损失。
具体而言,基于机器学习的预测性维护有以下原理和实施步骤:
1. 数据采集与存储
首先,需要收集设备的历史数据和实时数据,这些数据可以来自传感器、控制系统等源头。数据可以包括设备的运行状态、温度、振动等参数。这些数据被存储在企业数据仓库或过程数据历史数据库中,为后续分析提供基础。
2. 机器学习建模
接下来,利用机器学习算法对数据进行训练和分析。机器学习模型可以根据历史故障数据和设备参数,学习和识别与潜在故障相关的模式和特征。例如,如果设备振动水平逐渐增加,模型可以判断这可能是一次即将发生的故障。
3. 设备诊断与预测
机器学习模型可以提供有关故障的贡献因素和根本原因的分析,辅助决策制定。一旦模型检测到潜在的故障,维护团队可以使用诊断工具确认故障的根本原因。这可能涉及拆解设备以检查各个组件或使用非破坏性测试技术。
4. 维护计划
根据诊断结果,维护团队可以制定和安排维护计划。这可能包括修复或更换损坏的组件、清洁和润滑设备、调整设备参数等。
5. 持续监控
基于机器学习的预测性维护是一个持续不断的过程,需要对设备性能进行持续监测。机器学习模型可以持续运行,随着运营变化而学习,并监测和预测未来的结果。维护团队可以利用这些洞察力,早期识别潜在问题,并采取措施防止它们成为严重的故障。
PreMaint是国内专注于设备管理领域的优秀解决方案,其预测性维护能力在多行业多企业已有多个实践应用。
在某航天发射塔的应用中,PreMaint基于应力应变、振动、温度、油液、电流电压等多源数据融合的预测性维护技术被采用。通过数字化健康管理,该系统提供了可与国外竞品相媲美的大型精密结构健康监测国产化的解决方案。这种预测性维护技术能够实时监测发射塔的各项指标,识别潜在故障迹象,并提供准确的预警信息,使维护团队能够及时采取维护措施,防止设备故障和非计划停机的发生。
图.火箭发射(Pexels)
在中海油的应用中,PreMaint基于工业互联的新一代信息技术,结合了“云边协同”工业机理和AI融合算法,为用户提供了机泵预测性维护整体解决方案。该系统利用多维特征提取算法和诊断分析工具,能够高效提取设备数据中的关键信息,并进行准确的故障诊断。通过预测性维护的实施,中海油实现了设备的智能预警和诊断应用,大大提升了分析诊断的效率,降低了设备故障和停机的风险。
图.海上钻井平台(Pexels)
总的来说,基于机器学习的预测性维护是一种创新的维护方法,能够通过分析设备数据和使用机器学习模型,提前识别设备故障迹象,并采取适当的维护措施,以阻止非计划停机的发生。
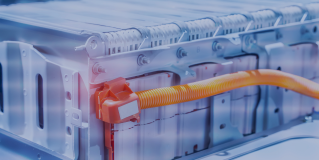
申请试用PreMaint预测性维护系统
延展阅读
<更多信息可关注公众号“设备工程”获取>