预测性维护在石油和天然气中的作用
发布时间: 2023年03月28日
标签:
在石油和天然气领域,设备的终身维护成本是很高的。设备都有必须进行的标准做法和常规维护手段。例如,维护团队根据设备制造商推荐的时间表检查设备(即使设备处于完美的工作状态),但定期停产意味着生产暂停。
图.海上钻井平台(Pexel)
一、计算预防性维护下的成本
预防性维护的成本并不低。通常情况下,每个工厂的生产环境不一样,这会导致同个设备制造商的设备寿命在不同工厂长短不一,导致设备需要维修或更换的时间点也不会一致。在设备手册中找到的建议维修计划是基于故障统计的,并没有考虑到在现实环境中,设备并不总是以平均速度失效。其次,还要考虑到下游作业的产量和停工时间。原油的提炼是一个市场驱动的过程,高需求增加了生产的紧迫性。当涉及到供应与需求的匹配时,更要确保避免设备故障影响生产,否则,设备故障导致的生产降低的成本就更高了。
二、预测性维护可以做什么
预测性维护(PdM)远比反应性或预防性方法更有效。工厂通常拥有用于PdM实践的设备,例如临时点检仪器,但这些设备通常在处理和共享数据方面能力有限。脱节的PdM技术的无效实施会在工厂层面造成问题。据统计,某国外海上钻井平台仅以82%的效率运行,而不是95%,这一差距代表了数十亿的生产和维护费用的损失。
市面上有些产品可以根据手动输入的阈值变量来远程监控设备。正确地设置这些参数需要有受过培训的人去收集、分析和输入适当的数据。如果参数没有配置好,或者不小心输入错误,或者在数据的海洋中被忽略,那么被监测设备就不能为生产提供应有的帮助,维护团队就会重新陷入被动的维护。
目前市场上各类单一分析技术的设备状态监测、预测性维护解决方案已逐渐成熟,例如有基于油液监测的、有基于红外热成像的、有自动巡检机器人的等等。PreMaint设备健康管理平台可以实现多源参数的融合,无论是DCS 或者IOT、第三方状态监测或者IT系统等,完成设备专属数据模型构建。PreMaint系统中不仅将专家经验和行业标准封装为模型算法,而且基于大量设备故障案例库和设备各环节数据,采用机器学习算法训练设备故障原因的智能诊断模型。通过AI算法,PreMaint专家系统可以定期生成设备健康专题的诊断报告,实现设备复杂多变工况下的立体监测、精准报警、故障诊断与预测维护,从而实现从监控到预警、故障诊断、维保维修处理的功能闭环,而不仅局限在设备管理的某个环节。
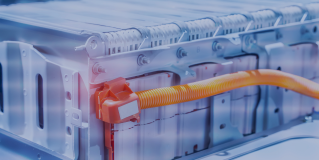
申请试用PreMaint设备健康管理系统
预测性维护策略的实现通常不是依赖单一的IT技术。更重要的是需要跟设备结构、工艺知识Knowhow结合,再通过大量的历史时序数据样本和维护工单数据,构建和训练出准确率达标的模型。PreMaint可以提供这些功能,基于设备的物理特性、物理规律,利用动力学规律建立机理模型,使用统计模型相关算法,结合时域数据、工艺数据、设备特征数据及各类报警预警数据等,构建设备等故障诊断模型和故障分析可视化服务,辅助设备工程师实现设备智能运维的场景闭环,直接按APP的提示,在特定时间去执行具体任务,让工程师更专注于解决关键问题本身。
PreMaint携手海油装备研发的基于边云智能协同的机泵群预测性维护解决方案,结合中海油设备专家的工艺知识,实现机泵群的在线状态监测、异常问题快速定位故障状态提前预警、故障智能诊断等,为机组异常原因分析及预知性维修提供强有力的数据支撑,有效提升中海油机组运行管理的技术水平。
延展阅读
<更多信息可关注公众号“设备工程”获取>