设备停机后如何进一步跟踪和分析-探究车间的真实情况
发布时间: 2023年04月19日
标签:
工厂可以被视作由人和设备等活动部件组成的系统。通常,人们希望在零问题、零事故的情况下,设备高效地将材料转换成产品。但我们都知道人类并不完美,设备也是如此。
在任何工厂或车间环境中,设备停机都会带来生产延误和损失。由于环境条件变化、材料质量不一致等因素的影响,工厂需要不断监控设备的运行状态并适时对其进行维护保养,以避免设备出现非计划停机的情况。
在本文,我们将介绍如何评估设备停机造成的损失、减少设备停机时间和提高效率的有效手段以及设备停机追踪和分析的工具,助力工厂减少设备停机时间、提高生产效率。
图.设备故障停机(PreMaint)
一、如何评估设备停机造成的损失
一般来说,设备停机带来的损失不仅包含停机期间的实际损失,还需从多个角度进行评估:
1. 生产损失成本评估:设备停机将导致生产线暂停生产,这意味着无法及时完成订单,从而导致销售收入损失。此外,生产损失还会导致生产物料浪费、过程中断和重新排程的成本等。因此,评估生产损失成本是一个重要的考虑因素。
2. 维修成本评估:设备停机可能需要进行维修或更换部件,这将导致额外的设备维护周期、清理费用、赶工加班所需额外支付的工资、人工成本和零部件成本。这些成本也需要纳入评估中。
3. 设备可靠性评估:设备停机可能会降低设备的可靠性和寿命。因此,评估设备停机对设备可靠性和寿命的影响也是很重要的。
4. 生产计划评估:设备停机将影响生产计划的制定和执行,需要重新调整和安排生产计划,这将导致额外的生产计划和排程成本。
5. 客户满意度评估:如果设备停机导致订单延迟或无法按时完成交货,将影响客户的满意度。因此,需要考虑客户满意度的影响。
评估设备停机造成的损失需要考虑多方面的因素。对这些因素进行综合评估可以帮助企业更好地了解设备停机带来的影响,并制定有效的措施来减少损失。
图.综合评估设备停机损失(PreMaint)
为了全面地评估停机带来的影响,您需要一则准确记录停机事件的日志,要想充分利用该日志,您应该在日志中记录以下内容:
1. 停机时间和原因:记录停机开始和结束的时间以及停机原因,这有助于追踪和识别设备故障和停机原因。
2. 生产数量和计划:记录停机期间应生产的数量和计划,以及实际生产的数量和计划。这有助于确定生产损失和重新安排生产计划。
3. 设备维护记录:记录设备的维护记录,包括维护计划、维护时间和维护人员等。这有助于确定设备的可靠性和维护效果。
4. 维修记录:记录停机后需要进行的维修记录,包括需要更换的零部件、维修时间和维修人员等。这有助于确定维修成本和维修效果。
5. 设备性能数据:记录设备的性能数据,如生产速度、温度、压力等,以帮助确定设备停机的原因和解决方法。
6. 操作员记录:记录操作员的记录,包括设备调整和操作过程中的问题和异常。这有助于确定操作员技能和设备使用情况。
记录以上信息可以帮助企业全面了解设备停机对生产带来的影响,进而制定有效的措施来减少停机时间。比如根据停机原因和维修记录,采取预防性维护措施;根据操作员记录,进行培训和技能提升;根据设备性能数据,对设备进行调整和优化等等。
二、减少设备停机时间和提高效率的有效手段
1. OEE数据车间可视化
在工厂接入数据后,建议第一步可以直接在车间展示OEE数据,这样做有助于减少设备的停机时间。因为当员工能了解到设备的实际情况,他们会更有动力去改善它。当停机发生时,他们也可以第一时间获取到信息,并采取行动。
2. 定位并解决导致设备停机的最主要原因
在积累了一定的数据量之后,可以根据设备运行历程来定位设备停机的最主要原因,并将精力集中在解决该问题上。可以参考以下工具来解决问题:
①.5why分析法(对一个问题点连续以5个“为什么”来自问,以追究其根本原因);
②.与生产人员进行短会,以获得解决思路;
③.定期组织与生产人员的站会,提出问题并协同解决;
3.解决更复杂的问题
要解决更复杂的问题,有许多行之有效的方法。以下是一些我们推荐的方法:
-根本原因分析法:一般包括以下流程①定义问题;②分析问题;③计划解决方案;④实施解决方案; ⑤控制与追踪;
-A3问题解决法:把问题的源头,分析,纠正和执行计划放在一张A3的纸上表达出来,并及时更新或报告结果;
图.A3报告法-设备停机分析报告(PreMaint)
-快速换模法(SMED):是将模具的产品换模时间、生产启动时间或调整时间等尽可能减少的一种过程改进方法,可显著地缩短机器安装、设定换模所需的时间。
-精益六西格玛(Lean Six Sigma):精益生产与六西格玛管理的结合,其本质是消除浪费,一般采用项目管理的方式,采用DMAIC流程分析技术——定义(define)、测量(measure)、分析(analyze)、改进(improve)、控制(control)来实现产品和服务质量的持续改进。
-现场管理法(Gemba):生产管理者需要定期到生产现场进行检查和监督,发现问题并及时解决,以确保生产线的高效运转和质量控制。
4. 坚持不懈地不断改进
持续改进的挑战在于,一开始提出的问题很容易被解决,且改善效果显著。但一段时间后,工厂即使付出更多努力,也可能收效甚微,这将导致证明改进项目的合理性变得更加困难。对许多人来说,达到优良水平,并专注于监控设备情况以维持在这一水平是有意义的。但是,持续改进的主旨在于不断改进,不断提高目标,完成从“优良”到“卓越”的转变。
三、监测设备停机情况的方法
1. 手动记录跟踪
如果还没有开始跟踪设备的停机时间,可以尝试最简单的方法:手动记录。它的优点是:低成本、容易操作、所需培训较少。以下是常用的记录模板:
图.停机登记日志表(PreMaint)
如果正在手动跟踪设备停机时间,那么您可能已经意识到该方法的缺点,如录入和分析数据比较耗时、数据不准确、可能被人为篡改等。下一步,我们可以考虑开始使用自动化工具来记录和可视化停机时间。
2.使用专业的OEE数据分析软件
一个专业的OEE数据分析软件需满足以下条件:①可实时记录并存储生产数据(通过传感器和专用的工业物联网设备传输数据);②实时展示生产数据;③可提供输入额外数据的可能性,例如解释宕机发生的原因;④可访问历史数据,以满足分析要求。
图.OEE数据可视化(PreMaint)
东智PreMaint设备健康管理平台支持从多种维度进行各类数据的统计分析,包括管理角度的设备综合效率数据(OEE)、设备角度的MTTR、MTBF、故障率、停机时长等。此外,该平台还支持个性化选配指标,报告以方便理解阅读的图表形式呈现,让您通过数据发现公司的真正潜力,助力企业实现基于数据驱动的改进策略。此外,PreMaint的预测性维护方案支持使用传感器和数据采集技术监测设备运行情况,并分析数据以找出设备故障的原因。这可以帮助企业及时发现设备故障和异常,采取措施避免停机和提高效率。
四、总结
通过本文,您已经了解应如何评估设备停机带来的影响,以及可用来减少设备停机时间和提高效率的有效手段。如果您已经准备好使用设备停机监测和分析软件来帮助工厂减少停机时间、提高生产效率,填写下方试用申请,与我们联系。
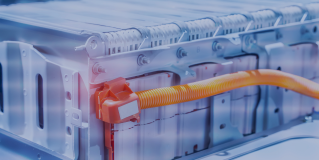
申请试用PreMaint设备健康管理系统
来源:@设备工程发布,内容部分参考网络,如有侵权,请联系删改。
延展阅读
>>什么是设备监测?设备监测有什么好处?
>>有了OEE实时数据,如何释放数据价值?
>>锂电材料工厂设备如何实现智能化运维?
<更多信息可关注@设备工程 公众号获取>